Cast Irons
What is cast iron?
Cast iron refers to a group of iron-carbon alloys with a carbon content exceeding two percent. It is known for its exceptional castability, which refers to the ease and efficiency with which a material can be cast or molded into a specific shape. Cast iron also offers wear resistance and heat retention properties.
Iron castings are made with various processes, such as the green sand process, resin sand process, shell mold, centrifugal process, permanent mold process, etc., depending on the specific features of the products and their intended applications.
Major elements include carbon, silicon, manganese, sulfur, and phosphorus. They are used in various applications such as engine components, pipes, cookware, and architectural elements.
Main Types of Cast Iron
Common types of cast iron include gray iron, ductile iron, and malleable iron, each offering unique properties suitable for different applications.
Gray iron
Gray iron, a common form of cast iron, is recognized for its distinctive gray appearance upon fracture, attributed to the presence of graphite flakes in the iron matrix. Widely used in various applications, gray irons are prized for their excellent castability, high damping capacity, and impressive machinability.
While generally acknowledged as having low to moderate strength, with tensile ranges typically between 20,000 psi and 60,000 psi, their exceptional damping and machining characteristics make gray irons a preferred choice for components such as engine cylinder blocks and brake drums in various engineering applications.
Ductile Iron Castings
Ductile iron, also known as nodular cast iron or spheroidal graphite iron, is a type of cast iron alloy that exhibits enhanced strength, toughness, and ductility, which is the degree to which a material can be stretched or bent without breaking.
Its distinctive makeup includes spherical graphite nodules, enhancing its flexibility and resistance to impacts. This type of cast iron is created by adding small amounts of magnesium to molten iron before casting, causing the formation of these nodules during solidification. They have moderate machinability and higher strength with tensile ranges from 60,000 psi to over 150,000 psi.
Overall, ductile iron offers a balance of strength and ductility, making it well-suited for a wide range of applications, including pipes, automotive components, and machinery parts. It is valued for its ability to withstand stress and deformation without fracturing.
Common Ductile Iron Grades
60-40-18
65-45-12
80-55-06
100-70-03
Mining & Aggregate Industry Components
Oil & Gas Components
Compressor Components
Automotive Components
Hydraulic Cylinder and Actuator Components
Rolled Ring
Forgings
Die Forgings
Non-Ferrous Castings
Cast Irons
Steel Sand & Investment Castings
Elevate your casting experience with CAB – contact us now to unlock limitless possibilities for your business
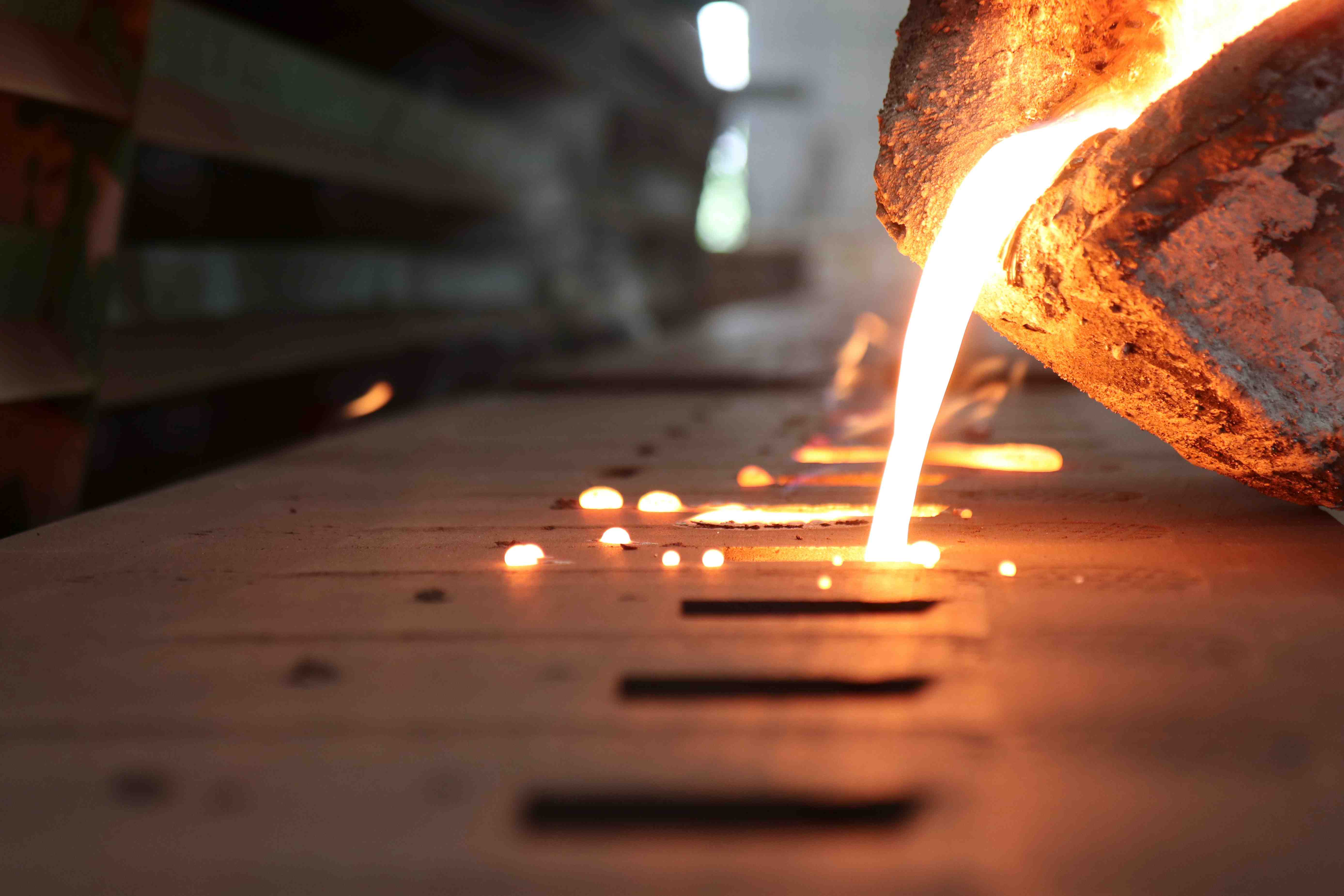